General Electric and 3D Printing
I sat down yesterday with Richard Rainey and Stephen Shackelford at General Electric global headquarters in Fairfield, CT. Initially, we were to discuss the Lightweight & Modern Metals Manufacturing Institute (LM3I) of the National Network for Manufacturing Innovation (NNMI). But with the Rhode Island coalition merging into the Draper Labs led group in Cambridge, our conversation turned into a lively discussion of how GE uses 3D printing.
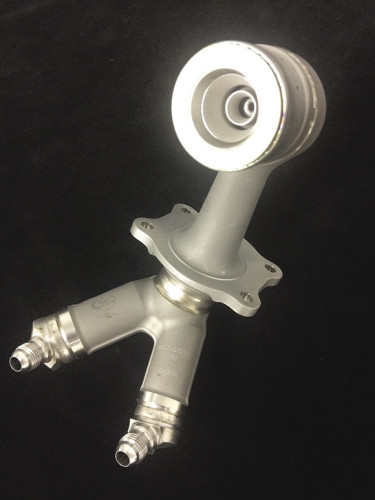
The above fuel injector recently made waves in the media (not to be confused with these angle brackets. This piece used to require 18 disparate parts that had to be welded together. In comparison, the additive manufactured version is printed in one single piece. Early lab testing found that the new part is five times as durable and results in superior fuel economy due to more uniform fuel spray. Many “boring” parts will also be printed for the LEAP engine, with 3D printing enabling a reduction of weight by over 1000lbs per engine.
However, it’s not just GE Aviation that is pushing innovative uses of 3D Printing. GE uses over 300 3D printers across numerous divisions. GE Healthcare is 3D printing parts for ultrasound probes, cutting costs by up to 30%. GE Global Research is developing a process for 3D printing ceramic matrix compound, a material with the heat resistance of ceramics and the strength of metal. GE Power and Water has used the technology for producing a cooling shroud for gas turbines.
3D printing allows you to make that product right the first time, it allows you to make it from the core up so you basically don’t have as much waste, the tooling is cheaper the cycle time is faster, and that is the holy grail. If I thought all that 3d printing could do was your shoes, I wouldn’t be talking about it quite as much as I am today. If you can make unique shapes with with high tech materials in a quick period of time then that is worth my time. That is worth a lot of investment.
- Jeff Immelt, CEO of General Electric
Richard, Stephen and I also discussed emerging intellectual property issues that result from 3D printing. The company is all too aware that once a design leaks, there is no rolling back the clock. As the recent Morris Technologies acquisition demonstrates, GE wants to keep 3D printing in house. Time will tell if large, centralized manufacturers will be forced to embrace the decentralized promise of local 3D fabrication.
← Back to Writing